Even before the Corona pandemic, digital commerce was on an unstoppable upward trend. But the years 2020 and 2021 will certainly go down in history as decisive drivers towards full digitalisation in e-commerce.
Because the continuing boom not only affects sales figures and increases in turnover. It is also proving to be a challenge for high-performance e-commerce logistics, which requires strong and sustainable solutions that enable continuous communication between the online shop and the warehouse management system.
What strategies are required? What technological support do online retailers with their logistics or fulfillment service providers need to cope with the new requirements? What role does E-Commerce-Beratung play in the success of future-proof online commerce? In this article, we have summarized the most important considerations for you.
When the eCommerce boom becomes a logistical problem
Continuous communication between online store and warehouse management systems ideally takes place without media discontinuity via the interfaces of the warehouse management software. However, particularly in warehousing and logistics, it has become apparent amid the boom that the essential processes have so far been carried out digitally and automated at a deficient level. Operations that a company could quickly scale with technological support are all too often still carried out manually or analogously.
Given that the volume of orders and shipments in online retailing has not only increased enormously, along with rising demands in terms of quality and service, it also becomes apparent just how adverse the effects of these omissions can be. To illustrate this with an example: online stores that have failed to cope with the increased order volume caused by the Corona pandemic are currently facing massive "fire" from negative reviews from customers complaining about incorrect or late deliveries.
Warehousing1 identified this problem early on and therefore developed a high-performance integration solution for WH1+ that smoothly connects store systems to warehouse management systems, even with extremely high order volumes and/or fluctuations, and automatically transmits data that can then in turn be transparently viewed by the customer in a real-time dashboard.
Thinking the supply chain from the end: warehouse software and technologies as smart support for automated logistics processes
Both private and B2B final customers are upset that the presentation and ordering processes are digital from start to finish. The part of the sales process that is visible to customers and clients is therefore optimally organized.
Yet, as soon as it comes to delivery, the chain falls apart at its weakest element. Namely, whenever there is no digital strategy worth mentioning in areas such as picking, packaging, addressing, transport, and returns management.
For this reason, a high-performance eCommerce logistics system does not focus unilaterally on smooth communication with customers and the order process. Instead, it pursues end-to-end communication between all the players involved - including and especially those who work in the background to ensure that the supply chain is not interrupted. The WH1+ dashboard thus allows inventory, shipment, and returns data to be viewed in real-time at any time and to integrate into customer communications. At the same time, issues can be spotted early on through email notifications and resolved promptly.
Only if the entire warehouse system, all the way to observing the customer and item structure, is geared to Internet commerce instead of following outdated analog processes can the desired performance, scalability, and communication be achieved. This has the advantage of bringing the ratio of customer orders to cost factors into a balance that is favorable for the company.
Making warehouses and logistics fit for the challenges of online retailing therefore means thinking about and organizing the supply chain from the end. This includes
• abandoning paper in the office and mapping all processes and tasks digitally so that control is internal and based on relevant data.
• effectively integrating all players into shipping logistics - up to and including the shipping service provider.
• using an intelligent warehouse software that communicates with devices used in the warehouse as technological support, such as data collection or pick-by-voice picking.
Commissioning processes as an opportunity
In addition to communication that automatically records all internal processes, selecting the appropriate picking method is a suitable way to turn current challenges into opportunities. Pick & Pack processes, in particular, are increasingly coming into the spotlight as they allow goods to be packed directly into the shipping carton.
However, unless this is controlled by software and automated, the error rate will be high, and the process will prove to be highly prone to failure. The savings in time, staff, and warehouse capacity are then canceled out by typical errors common in warehouse logistics without a smart recording of inventory and shipping.
Even minor errors often cause significant damage. For example, when the faulty goods are repeatedly packed, addresses are mixed up, inappropriate packaging sizes are selected, or returns can only be recorded with difficulty.
Leverage consulting and technological support for optimal logistics solutions
Which logistics solution is the best for your industry and your company? How can processes be automated and digitalized to make all tasks effectively with minimal effort? Are technical solutions such as the Pick & Pack process or AutoStore ideal to implement in your company?
If you are faced with these questions and want to examine and modernize your warehouse technology and warehouse logistics, you should rely on independent and unbiased advice. After all, every warehouse is individual, and all processes should always be capable of flexibly adapting to current requirements.
Regardless of the size of your company, you will thus keep your costs per order low and master all the challenges of digital commerce through the optimal interaction of human productivity and smart technology.
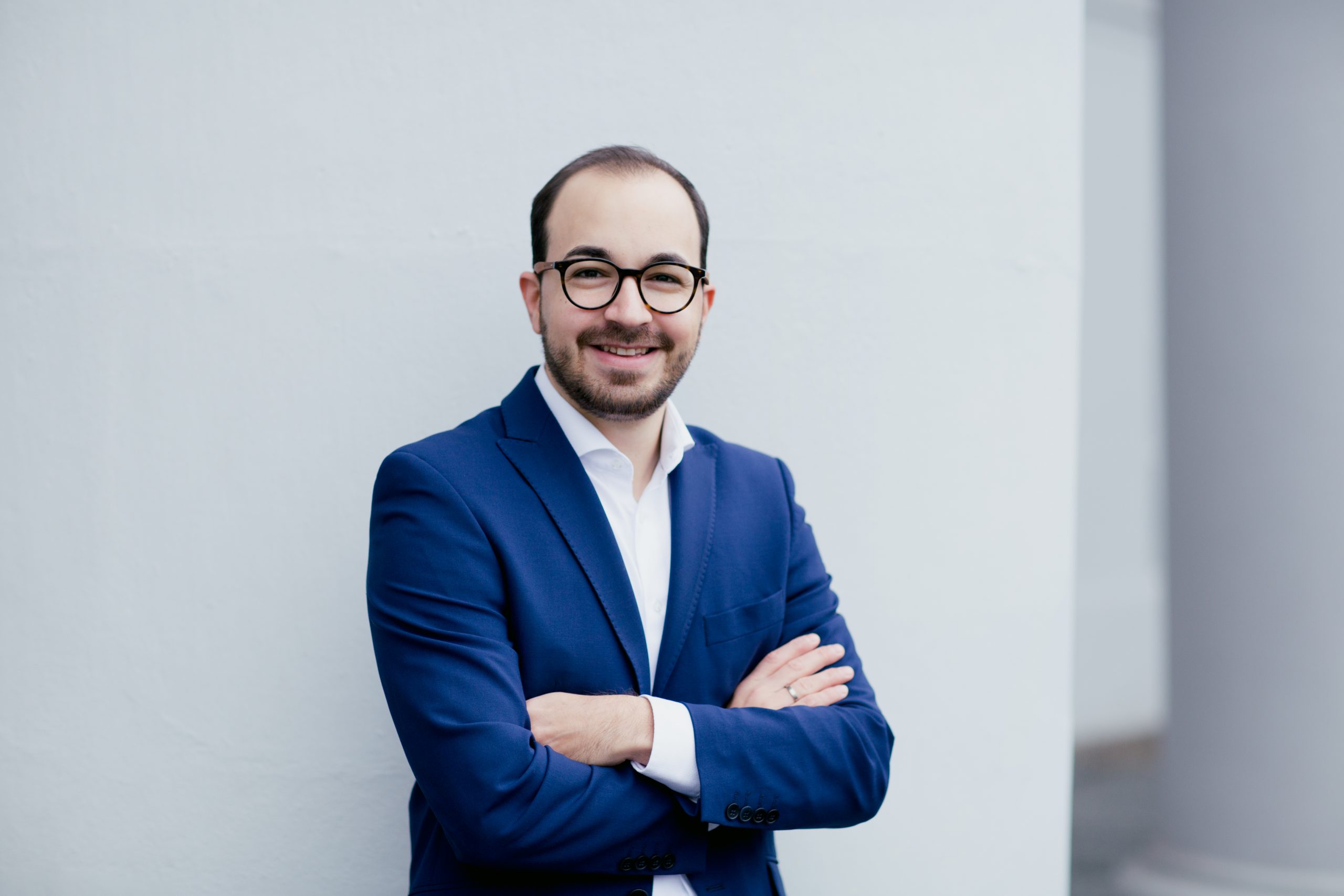
This article has been written in cooperation with Marcel Wilhelms.
Marcel Wilhelms is Managing Director of EPG Consulting and has more than ten years of experience in logistics consulting. His strengths reside in national and international project management, from the planning and implementing warehouse and logistics concepts to material flow analysis and the realization of optimization potentials. EPG Consulting offers neutral, manufacturer-independent logistics consulting with the goal of supply chain optimization.
You have an eCommerce and are looking for a performant solution for your logistics? Just ask us and we will see how we can help you!
Warehousing1 always has the right provider with a network of over 850 locations. In addition, any store system can be connected easily and efficiently via the WH1 API.